Hersey Clutch Company’s response to COVID-19
Leave a CommentCOVID-19 has caused widespread sickness, death, economic instability, and untold fear. However, it has shown, despite our differences and current polarization, that we can still make personal sacrifices to keep our communities, our country, and our world healthy and safe. This is a time for optimism and stoicism and it’s an opportunity to learn how to come together to solve important problems.
The Hersey Clutch Company joined many others who have retooled their production lines to offset the strained demand for medical equipment. As a family business having personal ties to medical professionals working in ICUs, it was important to use our skills and equipment to help them and many others.
Face Shields
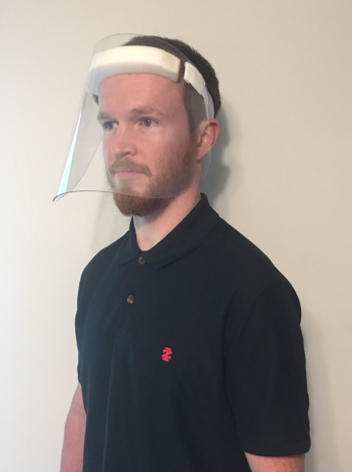
Our flexible in-house manufacturing capabilities enabled us to rapidly pivot to turn raw materials into PPE. We used our OMAX 5555 Waterjet to cut PETG sheet for the shield itself and 1” thick urethane for forehead foam. With our nesting software and our in-house developed modular fixturing, all the parts for the shields were cut within two days of finalized design. The first batch was delivered within one week of inception of the project.
Our local police departments in Brewster, MA was one of the organizations that received our face masks. They expressed their appreciation in a Facebook post:
“A huge thank you to Dick Hersey and Brian Baronousky-Chin from Hersey Clutch Company in Orleans. They made full face shields and donated them to The Brewster Police Department. These face shields will undoubtedly protect our officers as we continue to work during this pandemic. Thank you!”
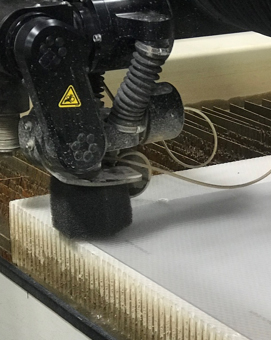
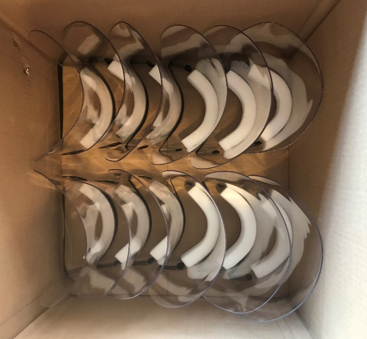
Getinge
Getinge, a customer we have worked with for years, is a global leader in the field of Surgical Workflows. The sterilizers and autoclaves they manufacture play an important role in enabling hospitals to maximize their capacity to treat as many patients with the best possible care. We were able to quickly to supply them with parts they needed in a matter of days to deliver more sterilization machines quickly to deploy them to help protect healthcare workers.
Service Specialties/Liftco
Another customer of ours, Liftco, produces mobile command centers for government and military use. Our overload protection products are used on their vehicles to prevent equipment from becoming damaged in transit or during setup.
In response to the pandemic, they converted their mobile command centers to rapid response vehicles for civilian use to deal with the increased health care demand. As an essential manufacturer we were able to help in their efforts by getting them components for their important vehicles quickly.
Moving forward
As we continue our efforts to end Covid-19, we have all learned lessons from the roles we have played that can prepare us to respond more effectively to similar events in the future.
As manufacturers, we will be ready to respond to the next crisis with new solutions and experience to build the products that the world will depend on to stay healthy and safe.
Case Study: Canadian Renovations & Restorations Inc. 1FCDC Clutch
Leave a CommentDelivering power with protection: Protecting drive systems to increase renewable energy production
The Company
Canadian Renovations & Restorations Inc. (CR&RI) provides a resource for renewable energy systems including installation, management, monitoring, and maintenance of solar power generators. CR&RI manages, monitors, and maintains commercial rooftop and many dual-axis sun-tracking ground mounted solar generation stations located in local and remote regions of Ontario, Canada. Dual-axis solar generators track the sun east to west and rotate to match the declination of the sun during the day. Solar tracking increases production, and thus revenue, by 40% over fixed tilt solar systems.
Dual-axis solar tracker installation (13.0 kW)
The Problem
While dual-axis trackers greatly increase solar power production efficiency and revenue, they cost more and are more maintenance intensive than fixed tilt non-moving systems. CR&RI accepted the contract to maintain an existing portfolio of solar generators that were under engineered for the wind loading these trackers would experience. Because of this, solar arrays were shearing motor shafts and stressing gearboxes thus arresting the tracking function and thereby reducing revenue and adding cost to the Owners investment. Compounding the problem, the stations were built in remote locations, and when a solar tracker stopped functioning, it would take as much as 4 to 5 hours to reach and repair the inoperable mechanism.
The solar trackers unplanned downtime was robbing the Owners of revenue and reducing return on investment. A 20-year contract with the Ontario government pays the owners a fixed specific rate for power generation for the length of the contract. Every watt missed is a watt lost in return on the investment of an expensive solar tracker. For the Owners, Canadian Renovations & Restorations Inc. needed a solution that would make the drivetrains of the solar trackers more reliable.
A sheared motor shaft still visible in the slew drive (east to west movement)
The Solution
Having endured broken motor shafts for several years, the Owners relied on Canadian Renovations & Restorations Inc. to find a solution that would integrate between the existing motor shaft and the sun tracking drive mechanism of these solar trackers. The motor shaft was constrained in size to match the size of the slew worm drive that operated the east/west bearing movement. The alternative of changing out the slew drive, allowing for a larger motor shaft, required an expensive upgraded slew drive bearing, along with a crane and crew to lift the solar matrix for removal and reinstallation and was cost prohibitive for a portfolio of solar trackers. After much research and discussion, with many companies and their representatives, on this very custom application and requirement, no solution was found until CRRI turned to Hersey Clutch Company for a drivetrain solution. After a long and thoughtful discussion with Dick Hersey, a 1FCDC friction clutch was decided on for the application.
The bidirectional torque limiting friction clutch functioned as a direct coupling between the motor and the gearbox. It was able to prevent excessive forces from wind load force being fed back into the gear box and motor and was able to begin driving the solar panels to face the sun immediately. Downtime was eliminated.
The HCC friction clutch employs a simple design that provides high reliability and achieves greater functionality as far more expensive clutches reviewed by CR&RI. The high function available, at such an economical price point, provided a cost effective retrofit for all their dual-axis solar tracking power generators.
Test fit of the 1FCDC friction clutch with clutch exposed for visibility.
The solar tracker with the retrofitted clutch enclosed.
Retrofitting their motor to gearbox connection required a unit that fit within the limited space of their configuration. Our in-house engineering and manufacturing capabilities enabled us to accommodate their specific drive needs with a custom developed output shaft. Using SolidWorks Simulation, we were able to rapidly iterate the design to optimize the output shaft geometry to maximize strength within the small package. We delivered a design suited to their specific conditions within days.
The stress gradient shown for the final custom output shaft.
FEA meshing
Conclusion: Delivering power with protection
Increasing the reliability of the dual axis solar tracker has paid off. Since CR&RI implemented Hersey Clutch Companies friction clutch, there has been zero unplanned downtime because of this issue. The solar trackers have operated as expected and production is commensurate with local solar statistics.
After seeing the dramatic results of using a torque limiting clutch on their test dual-axis solar power generator, Canadian Renovations & Restorations Inc. retrofitted all the solar dual-axis tracker in the same way.